What is Porosity in Welding: Necessary Tips for Achieving Flawless Welds
What is Porosity in Welding: Necessary Tips for Achieving Flawless Welds
Blog Article
Porosity in Welding: Identifying Common Issues and Implementing Best Practices for Avoidance
Porosity in welding is a prevalent problem that typically goes unnoticed until it causes significant issues with the honesty of welds. In this discussion, we will certainly discover the essential aspects adding to porosity formation, examine its harmful results on weld performance, and go over the best techniques that can be adopted to minimize porosity event in welding processes.
Usual Root Causes Of Porosity

An additional frequent perpetrator behind porosity is the existence of contaminants on the surface of the base steel, such as oil, grease, or corrosion. When these contaminants are not properly gotten rid of prior to welding, they can vaporize and end up being entraped in the weld, causing defects. Utilizing dirty or damp filler materials can introduce pollutants into the weld, adding to porosity problems. To mitigate these typical root causes of porosity, detailed cleaning of base steels, appropriate securing gas choice, and adherence to optimal welding parameters are essential techniques in achieving premium, porosity-free welds.
Impact of Porosity on Weld Top Quality

The existence of porosity in welding can substantially compromise the structural honesty and mechanical properties of bonded joints. Porosity produces voids within the weld metal, damaging its total stamina and load-bearing ability. These gaps work as stress focus factors, making the weld a lot more vulnerable to splitting and failure under used lots. Additionally, porosity can minimize the weld's resistance to rust and other ecological aspects, better diminishing its longevity and performance.
Welds with high porosity levels have a tendency to exhibit lower influence stamina and reduced capability to flaw plastically prior to fracturing. Porosity can restrain the weld's capacity to properly transmit pressures, leading to premature weld failing and possible security dangers in crucial structures.
Ideal Practices for Porosity Prevention
To enhance the architectural stability and quality of welded joints, what details procedures can be implemented to lessen the incident of porosity during the welding process? Using the correct welding method for the details product being bonded, such as readjusting the welding angle and weapon position, can additionally prevent porosity. Routine inspection of welds and immediate remediation of any concerns recognized during the welding process are important methods to prevent porosity and produce premium welds.
Relevance of Appropriate Welding Techniques
Carrying out proper welding techniques is paramount in guaranteeing the architectural stability and top quality of bonded joints, developing upon the foundation of efficient porosity prevention steps. Welding strategies directly influence the general stamina and resilience of the welded framework. One essential facet of correct welding methods is keeping the right warmth input. Extreme heat can lead to enhanced porosity as a result of the entrapment of gases in the weld pool. On the other hand, insufficient warm may result in incomplete blend, producing prospective powerlessness in the joint. Furthermore, utilizing the appropriate welding specifications, such as voltage, existing, click resources and travel speed, is essential for accomplishing sound welds with marginal porosity.
Moreover, the option of welding process, whether it be MIG, TIG, or stick welding, must line up with the specific demands of the job to make sure ideal outcomes. Proper cleaning and preparation of the base metal, in addition to picking the appropriate filler product, are likewise important elements of proficient welding techniques. By adhering to these finest practices, welders can reduce the risk of porosity formation and generate premium, structurally sound welds.
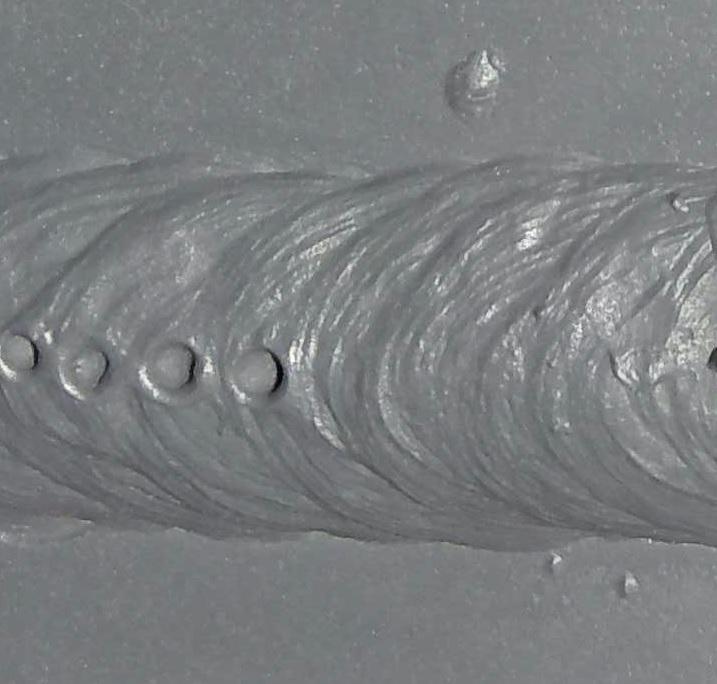
Testing and High Quality Control Actions
Examining treatments are vital to identify and stop porosity in welding, guaranteeing the toughness and toughness of the final product. Non-destructive screening methods such as ultrasonic testing, radiographic screening, and visual examination are typically used to identify possible issues like porosity.
Performing pre-weld and post-weld assessments is likewise important in keeping quality assurance standards. Pre-weld examinations involve verifying the materials, devices settings, and sanitation of the work location to stop contamination. Post-weld evaluations, on the various other hand, examine the last weld for any type of defects, including porosity, and confirm that it fulfills defined standards. Implementing an extensive quality assurance plan that includes detailed testing procedures and evaluations is extremely important to reducing porosity problems and guaranteeing the general top quality of bonded joints.
Conclusion
To conclude, porosity in welding can be an usual problem that affects the quality of welds. By identifying the common root causes of porosity and applying ideal practices for prevention, such more helpful hints as appropriate welding methods and testing measures, welders can ensure top quality and dependable welds. It is vital to prioritize avoidance techniques to minimize the occurrence of porosity and maintain the integrity of Check Out Your URL bonded structures.
Report this page